Ray Hahn
The Whole Story of the Needle's Hole
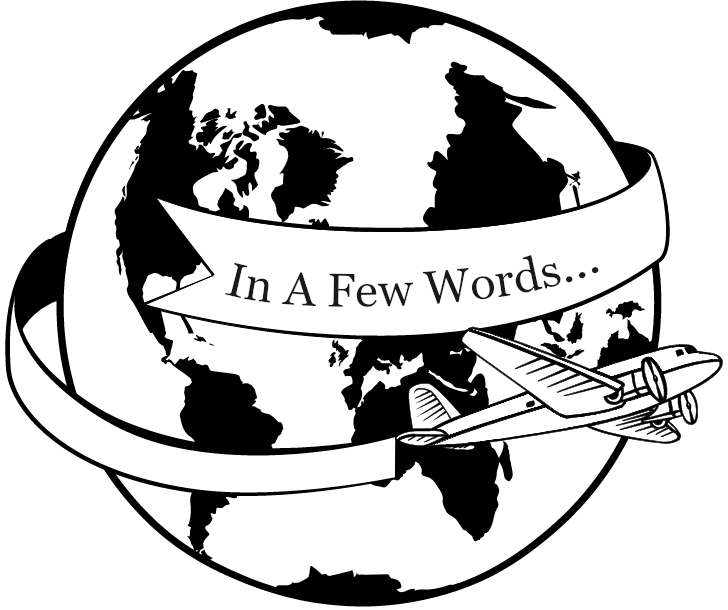
Recently a card in an online auction caught my attention. It represented a new challenge and I couldn’t resist. I can, without fear of contradiction, say that until today I knew absolutely nothing about needles, except, I was able to identify one when I saw it. I knew they are small, they are difficult to pick-up except when you step on one, and they are very sharp. I also knew it hurts like the dickens when the pointed end of a needle finds your finger-tip.
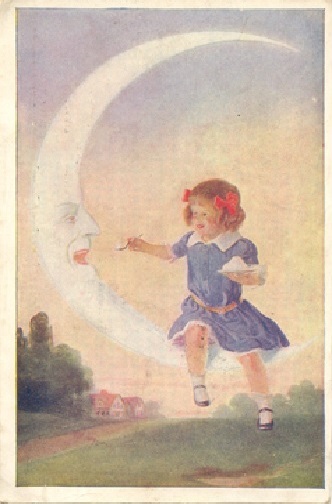
The card I mentioned is a typical white-border card from an era that spanned the years 1927 to 1935, see left – the young girl sitting on a crescent-moon. Such cards were frequently used to advertise sewing supplies, but that is really of little consequence to this story. Although it is signed by its user from Ithaca, New York, and mentions a product, it should not be considered an advertisement because there is no illustration of a product; only the mention of a company name. The message asks the recipient to reply to the sender with an opinion regarding the “Standard Needle” manufactured by the Central Needle Company. [I was unable to learn much about Central Needle except that as long ago as 1885, the company enjoyed a basic monopoly over the manufacturing and sales of needles in the United States. (See: New York Times, July 7, 1885.)] From reading the message it is safe to assume that other cards like it were sent to seamstresses, quilt makers, and others who used needles regularly. There is one remaining characteristic that needs mentioning – the message is sewn to the postcard. A detail from the card, shown right, is enlarged, and yet it is still difficult to see, but trust me, there is actually thread running the length of the card.
There is no reason why I should have known about the “sew worthiness” of needles. Durability and purpose both depend on quality, sharpness, straightness, needle puncture pattern or any of a half-dozen other characteristics, and even though I have now experienced a fairly steep learning curve with regard to needles, I will leave that story for someone else to author. My wife, Marie on the other hand can tell the size, shape and purpose for which a needle was designed just by looking at it.
Before I write more, I beg my reader to remember that there are many ways to manufacture needles, and I am reporting on only the first mechanized method invented to make hand use needles – the making of sewing machine needles is a story for another day.
The “hole” story is . . . needles are made from steel wire that is cut to a length equal to two identical needles. The wire is first straightened. Both ends are sharpened – my mind’s eye sees a machine much akin to a pencil sharpener. The wire is then “pressed” in the exact center to cause a flat space, an area into which two identical sized holes are “punched.” The holes are then smoothed to eliminate any sharp edges that could cut a thread. Upon completion of the smoothing, the needles are fired (to increase hardness), rolled (to perfect roundness), and polished (to prevent oxidation). Then, a second piece of wire is threaded through one hole and back through the second hole, making it possible to cut the needles apart and have two finished products hanging together on that second wire. Lastly, the needles are inspected, packaged and shipped to your favorite sewing shop – where they are priced for much more money than they were in 1885.
And, I guess, in some cases they are used to sew messages on postcards. Yep, that’s the “whole” story.